Hardware Brackets: Strengthening Industries with Customized Solutions
Hardware brackets are essential components in industrial settings, providing structural support, wei…….
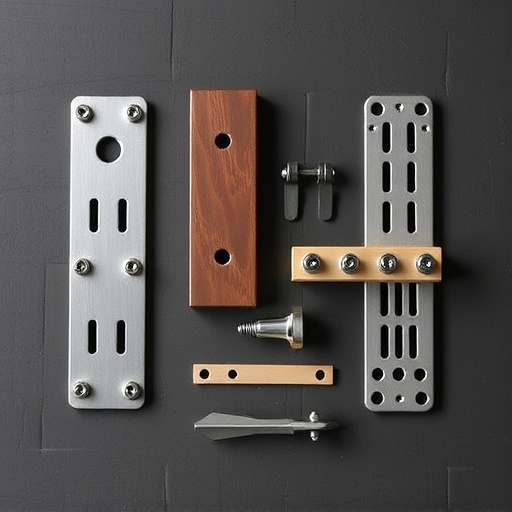
Hardware brackets are essential components in industrial settings, providing structural support, weight distribution, and component security. They are crucial for machine stability, performance, and longevity, facilitating efficient assembly, maintenance, and operations. The choice of materials and designs is informed by specific industry needs, with engineers considering factors like load capacity, environmental exposure, and customization to optimize system performance. Hardware brackets are indispensable in automotive, aerospace, and manufacturing sectors, ensuring equipment durability and efficiency. Future advancements in smart sensors and 3D printing technology promise to further enhance their capabilities.
Hardware brackets play a pivotal role in various industrial applications, offering crucial support and structural integrity. This article delves into the multifaceted world of hardware brackets, exploring their diverse uses, materials, and design considerations. From manufacturing to construction, these versatile components enhance durability and safety. We examine industry-specific implementations, safety standards, and future trends shaping innovation in hardware bracket technology, underscoring their indispensable role in modern industrial landscapes.
- The Role of Hardware Brackets in Industrial Applications
- Types and Materials Used for Strength and Durability
- Common Industries Leveraging Hardware Brackets Effectively
- Design Considerations for Customized Bracket Solutions
- Safety and Compliance Standards in Industrial Hardware Brackets
- Future Trends Shaping the Industrial Use of Brackets
The Role of Hardware Brackets in Industrial Applications
Hardware brackets play a pivotal role in various industrial applications, offering unparalleled versatility and structural integrity. These essential components are designed to securely fasten, support, or connect different parts within complex machinery and equipment. In manufacturing settings, for instance, hardware brackets ensure the stability of production lines, allowing for efficient assembly and operation.
By distributing weight evenly and preventing component shift, hardware brackets contribute to enhanced machine performance and longevity. They are particularly crucial in environments where heavy loads, extreme temperatures, or corrosive elements pose challenges. With their ability to facilitate adjustments and repairs, these brackets enable quick maintenance and ensure optimal functionality, making them indispensable for maintaining industrial operations’ efficiency and reliability.
Types and Materials Used for Strength and Durability
In the industrial sector, the choice of materials and components is critical for ensuring strength and durability. One essential element often overlooked but pivotal to overall structural integrity are hardware brackets. These brackets serve as connectors, distributing weight and preventing stress concentration in various industrial applications.
The types and materials used for hardware brackets can vary widely depending on the specific industry needs. Common choices include steel, known for its high strength-to-weight ratio and corrosion resistance, often galvanized for added protection. Aluminum is another popular option, offering lightweight yet durable performance, ideal for environments where weight reduction is crucial. Additionally, specialty materials like stainless steel are employed in harsh conditions requiring superior corrosion resistance. The selection process involves considering factors such as load capacity, environmental exposure, and the need for customization to fit unique industrial layouts.
Common Industries Leveraging Hardware Brackets Effectively
In today’s industrial landscape, hardware brackets play a pivotal role in enhancing efficiency and durability across various sectors. These versatile components are commonly leveraged by industries such as automotive, aerospace, and manufacturing to secure and support diverse structures. In the automotive industry, hardware brackets are integral to assembly lines, facilitating the attachment of parts like engine components, body panels, and electronic systems. Aerospace manufacturers utilize them extensively for mounting and securing critical components within aircraft structures, ensuring both performance and safety.
In manufacturing, hardware brackets are indispensable tools for building robust machinery and equipment. They enable the secure attachment of moving parts, prevent loose connections, and contribute to overall stability. This is particularly crucial in heavy-duty machines where vibrations and external forces can be significant. By employing these brackets effectively, manufacturers can extend equipment lifespan, reduce maintenance needs, and ultimately drive operational efficiency.
Design Considerations for Customized Bracket Solutions
When designing customized bracket solutions for industrial applications, several key factors come into play. Hardware brackets form essential components in various machinery and equipment, demanding careful consideration to withstand specific load requirements and environmental conditions. Engineers must account for material selection, ensuring compatibility with the operational environment, whether it’s corrosive or extreme temperatures.
The structural integrity of brackets is paramount, especially when accommodating unique mounting configurations. Consideration should be given to the placement of mounting holes, bolt patterns, and the overall bracket geometry to ensure secure and stable attachment. Additionally, for dynamic loads, designing brackets with adequate flexibility and strength balance can prevent premature failure, enhancing equipment reliability.
Safety and Compliance Standards in Industrial Hardware Brackets
In the industrial sector, ensuring safety and compliance with standards is paramount when utilizing hardware brackets. These essential components play a critical role in structural integrity and worker protection across various applications. Compliance standards for hardware brackets involve meticulous attention to design, material selection, and manufacturing processes to meet stringent safety requirements.
Industrial hardware brackets must adhere to specific regulations, such as those set by occupational health and safety administrations. These standards dictate load-bearing capacities, dimensional specifications, and corrosion resistance to ensure the safe assembly and maintenance of industrial equipment. Regular inspections and quality assurance tests are crucial to verify compliance and maintain a robust safety framework in industrial settings.
Future Trends Shaping the Industrial Use of Brackets
The future of industrial applications is constantly evolving, and hardware brackets are no exception. As technology advances, new materials and manufacturing processes emerge, opening doors to innovative designs and enhanced functionality. One prominent trend is the integration of smart sensors into brackets, enabling real-time monitoring of structural integrity, load distribution, and environmental conditions. This data can be invaluable for predictive maintenance, ensuring critical components are replaced before failures occur, thereby improving safety and efficiency.
Additionally, 3D printing technology is revolutionizing bracket design and production. This allows for the creation of complex geometric shapes tailored to specific industrial needs, offering lightweight yet robust solutions. Customization at scale is another advantage, enabling manufacturers to produce unique brackets for specialized equipment or precise applications. These future trends promise to enhance the capabilities of hardware brackets, driving further efficiency and innovation across various industries.
Hardware brackets play a pivotal role in various industrial applications, offering essential support and stability. As technology advances, future trends in design and materials promise even greater efficiency and durability for these versatile components. Industries ranging from manufacturing to aerospace continue to leverage their benefits, ensuring safety and compliance with evolving standards. By understanding the types, materials, and design considerations, custom bracket solutions can be tailored to meet specific needs, solidifying hardware brackets’ place as indispensable elements in modern industrial landscapes.