Hardware Brackets: Setting Industry Standards for Quality and Interoperability
Hardware brackets, vital components in manufacturing and electronics, ensure structural integrity an…….
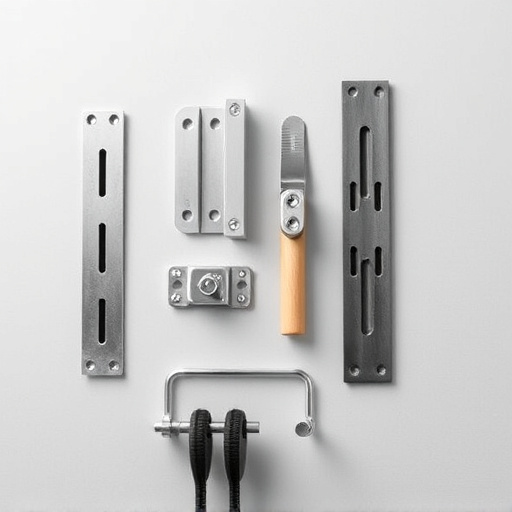
Hardware brackets, vital components in manufacturing and electronics, ensure structural integrity and connectivity. Adhering to industry standards guarantees their functionality, safety, and interoperability across systems. These standards dictate dimensional specifications, material choices (like aluminum or steel), and design features for easy installation and compatibility. Strategic material selection balances cost-effectiveness with structural integrity. Robust engineering practices, including quality control, ensure bracket reliability in diverse applications from automotive to aerospace. Industry standards promote innovation, efficiency, and interoperability, fostering economic growth and consumer trust in a digital age.
In today’s interconnected market, understanding industry standards is paramount. This article delves into the foundational role of hardware brackets in fostering quality and consistency across diverse sectors. We explore key considerations in designing these essential components, emphasizing material selection, engineering best practices, and interoperability for seamless integration. By examining the impact of standards on innovation and growth, we uncover how hardware brackets drive progress, ensuring products meet universal expectations while optimizing cost-effectiveness.
- Understanding Industry Standards: A Foundation for Quality and Consistency
- The Role of Hardware Brackets in Standardized Systems
- Key Considerations in Designing Industry-Standard Hardware Brackets
- Material Selection: Strength Meets Cost-Effectiveness
- Engineering and Manufacturing Best Practices for Brackets
- Ensuring Interoperability: Compatibility Across Industries
- The Impact of Standards on Innovation and Market Growth
Understanding Industry Standards: A Foundation for Quality and Consistency
Understanding industry standards is paramount in ensuring quality and consistency across various sectors, including manufacturing and electronics. In the case of hardware brackets, these are essential components that support and secure other parts together, making them subject to strict guidelines. Compliance with established standards guarantees not only functionality but also safety and reliability.
By adhering to these standards, manufacturers can ensure their products meet specific criteria for dimensions, materials, and construction methods. This uniformity facilitates interoperability, enabling different systems and components to work seamlessly together. For hardware brackets, this means they can be easily integrated into various devices, ensuring a standardized experience for users across different brands and models.
The Role of Hardware Brackets in Standardized Systems
In standardized systems, hardware brackets play a pivotal role by ensuring compatibility and modularity. These components facilitate the secure attachment of various hardware elements, allowing for easy installation and upgrades across different devices or platforms. By adhering to consistent bracket sizes and designs, manufacturers guarantee that compatible hardware can be seamlessly integrated, streamlining the assembly process and reducing potential errors.
Moreover, hardware brackets contribute to a more organized and efficient system architecture. They provide stability and alignment, especially in compact spaces, ensuring components are securely fastened and properly positioned. This standardization not only enhances the overall durability of the setup but also simplifies troubleshooting and maintenance, as technicians can quickly identify and replace faulty parts without navigating a labyrinthine web of diverse components.
Key Considerations in Designing Industry-Standard Hardware Brackets
When designing industry-standard hardware brackets, several key considerations come into play to ensure functionality, durability, and compatibility. The first step involves understanding the specific application requirements, such as weight capacity, environmental conditions, and the type of equipment to be mounted. This dictates the material selection—whether it’s lightweight aluminum for portability or robust steel for heavy-duty industrial use. The design should also account for easy installation and accessibility, incorporating features like pre-drilled holes and adjustable fasteners.
Moreover, hardware brackets must align with industry standards for safety and reliability. This includes adhering to dimensional specifications, ensuring proper clearances for equipment connections, and integrating secure fastening mechanisms. A well-designed bracket should allow for flexibility in orientation, enabling optimal equipment placement while minimizing strain on the mounting system. Additionally, considerations for aesthetic appeal and branding can enhance a product’s marketability, making it stand out in a competitive industry landscape.
Material Selection: Strength Meets Cost-Effectiveness
In the realm of industry standards, material selection for components like hardware brackets is a delicate balance between strength and cost-effectiveness. When it comes to hardware brackets, which often bear significant structural loads, choosing durable materials is paramount. Steel, for instance, offers exceptional tensile strength, making it ideal for robust applications. However, its higher cost can be a deterrent, especially in projects with budget constraints.
To bridge this gap, many manufacturers opt for alternative materials that provide adequate strength at lower costs. Aluminum, for example, has gained popularity due to its lightweight nature and corrosion resistance, albeit with slightly inferior tensile strength compared to steel. Balancing these considerations allows businesses to select materials that meet project requirements while adhering to industry standards and budget constraints.
Engineering and Manufacturing Best Practices for Brackets
In the realm of engineering and manufacturing, establishing robust best practices for hardware brackets is paramount to ensure product reliability and safety. When it comes to designing and producing brackets, several key considerations come into play. First and foremost, material selection is critical; high-strength alloys like stainless steel or aluminum are often preferred due to their durability and resistance to corrosion. Proper joint design and fastening methods are equally important to distribute load evenly and prevent failure points.
Additionally, consistent manufacturing processes and quality control measures are essential to maintain dimensional accuracy and consistency among brackets. This includes precise machining, strict tolerance standards, and regular inspections to catch any deviations from the designed specifications. These practices not only ensure that each hardware bracket meets the required industry standards but also contribute to overall product performance and longevity in diverse applications, from automotive to aerospace industries.
Ensuring Interoperability: Compatibility Across Industries
In today’s interconnected world, ensuring interoperability is vital for industries to seamlessly collaborate and advance. Hardware brackets play a crucial role in this regard, acting as the foundation for compatibility across diverse sectors. These components facilitate the integration of various systems, enabling data exchange and communication between different technologies. For instance, standard hardware brackets ensure that devices from multiple manufacturers can interface harmoniously, fostering innovation and efficiency.
Interoperability is not merely about technical connection; it drives economic growth by promoting the sharing of resources and knowledge. As industries evolve, adopting common standards for hardware brackets becomes essential to prevent fragmentation and encourage collaboration. This approach paves the way for smoother processes, reduced costs, and faster time-to-market, ultimately revolutionizing how sectors interact and thrive in a digital era.
The Impact of Standards on Innovation and Market Growth
Industry standards play a pivotal role in shaping the landscape of innovation and market growth, especially in sectors like hardware manufacturing. When well-defined standards are in place, such as those for hardware brackets, it creates a framework that both guides and restricts manufacturers’ creativity. On one hand, standards ensure compatibility and interoperability among different products, fostering seamless integration and encouraging consumer trust. This, in turn, drives market growth by facilitating easier product adoption and expanding market reach.
For instance, standardized hardware brackets simplify the design and production process for various electronic devices, leading to cost efficiencies and accelerated innovation. Manufacturers can focus on enhancing performance and adding unique features without worrying about compatibility issues. As a result, consumers benefit from a wider range of options, improved product quality, and competitive pricing. This balance between standardisation and innovation is crucial for maintaining a dynamic market while ensuring customer satisfaction and safety.
In conclusion, industry standards, particularly in the design and manufacturing of hardware brackets, play a pivotal role in fostering quality, consistency, and interoperability across diverse sectors. By understanding these standards and implementing best practices, manufacturers can create robust and cost-effective hardware brackets that drive innovation and market growth. The strategic selection of materials and adherence to engineering principles ensure durability and performance, while prioritizing interoperability facilitates seamless integration within standardized systems. Ultimately, adhering to industry standards positions manufacturers as key contributors to a thriving and interconnected marketplace.